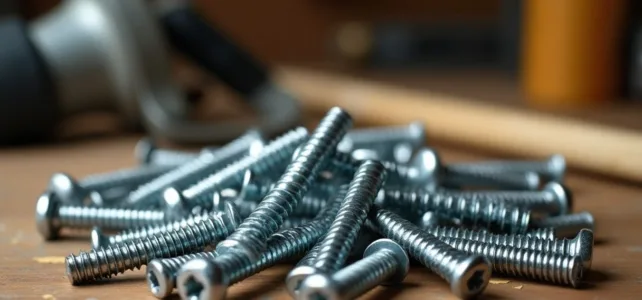
L’acier zingué est largement utilisé dans de nombreux secteurs industriels en raison de sa résistance à la corrosion. Cependant, il est naturel de se demander si, malgré son revêtement protecteur de zinc, cet acier est susceptible de s’oxyder. Pour répondre à cette question, il est essentiel de comprendre le processus de galvanisation et les divers facteurs qui influencent sa durabilité.
Compréhension de l’acier zingué
Composition de l’acier zingué
L’acier zingué est le résultat d’une combinaison de métaux où l’acier brut est recouvert d’une couche de zinc. Ce revêtement de zinc sert de barrière contre la corrosion. La protection est assurée par une réaction de type électrochimique où le zinc se sacrifie pour protéger le fer contenu dans l’acier.
Processus de galvanisation
La galvanisation est le procédé par lequel l’acier est immergé dans un bain de zinc fondu. Cette méthode, connue sous le nom de galvanisation à chaud, permet la formation de couches d’alliage fer-zinc qui augmentent la résistance à la corrosion. Le zingage électrolytique est une autre technique couramment utilisée, bien que moins épaisse, elle est souvent adaptée aux petites pièces.
Résistance à la corrosion
La résistance à la corrosion de l’acier zingué dépend de l’épaisseur du revêtement de zinc et de la qualité du procédé de galvanisation. Plus le revêtement est épais, plus la protection contre la rouille est durable. Le zinc, en tant que métal moins noble que l’acier, se corrode en premier, épargnant ainsi l’acier sous-jacent.
Durée de vie
La durée de vie de l’acier zingué peut atteindre jusqu’à 70 ans, selon les conditions environnementales. Les environnements maritimes ou les zones avec une forte pollution peuvent réduire cette durée. L’entretien et la maintenance régulière jouent également un rôle crucial dans la longévité du matériau.
Mécanisme de corrosion
Réaction électrochimique
La corrosion est principalement due à une réaction électrochimique entre le zinc et l’environnement extérieur. Cette réaction forme des produits de corrosion qui peuvent, à long terme, réduire l’efficacité de la protection.
Influence de la surface
La surface de l’acier zingué joue un rôle important dans la résistance à la corrosion. Plus la surface est lisse et exempte d’impuretés, meilleure est la protection. Un traitement de surface approprié avant la galvanisation est donc essentiel.
Épaisseur du revêtement de zinc
L’épaisseur du revêtement de zinc influe directement sur la résistance à la corrosion. Un revêtement plus épais offre une meilleure protection, bien que cela puisse augmenter le coût du matériau.
Effet du traitement de surface
Des traitements de surface supplémentaires peuvent être appliqués pour améliorer la protection contre la corrosion. Ces traitements incluent des peintures riches en zinc ou des revêtements organiques qui agissent comme une barrière supplémentaire.
Facteurs impactant la résistance à la rouille
Environnement
Les conditions environnementales, telles que l’humidité, la proximité de la mer, ou les niveaux de pollution, influencent significativement la corrosion de l’acier zingué. Un entretien adapté peut limiter ces effets.
Type d’acier
La qualité de l’acier utilisé affecte également sa résistance à la corrosion. Les aciers inoxydables, par exemple, contiennent du nickel et sont connus pour leur résistance supérieure à la rouille comparé à l’acier zingué.
Qualité du zingage
La qualité du zingage dépend des procédés utilisés. La galvanisation à chaud est généralement plus durable que le zingage électrolytique, bien que ce dernier soit plus approprié pour certaines applications spécifiques.
Maintenance et entretien
Un entretien régulier, tel que le nettoyage et l’application de revêtements protecteurs, peut prolonger la durée de vie de l’acier zingué. Il est essentiel de surveiller l’état du revêtement de zinc et d’effectuer les réparations nécessaires pour éviter la rouille.